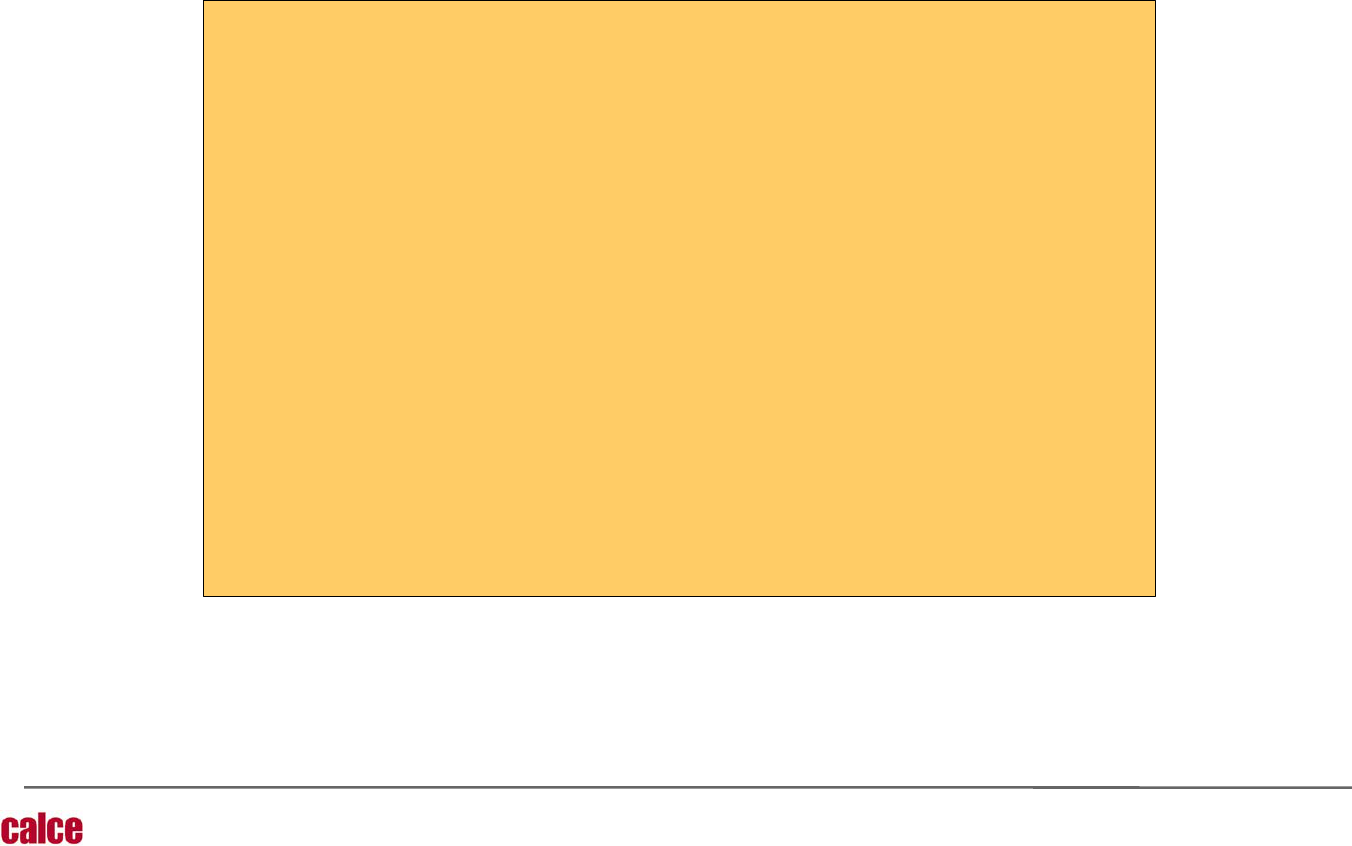
University of Maryland
© CALCE
46
Center for Advanced Life Cycle Engineering
CALCE Acknowledges its Sponsors and Customers
• ABB Switzerland Ltd.
• ACell, Inc.
• Advanced Bionics
• Agilent Technologies, Inc.
• America II Electronics, Inc.
• Anadigics, Inc.
• Ansaldo STS USA, Inc.
• Arbitron Co.
• ATV Semapp
• Austria Microsystems AG
• Avaya Global Operations
• BAE Systems Electronics &
Integrated Solutions
• Baker Hughes Inc.
• Bartlit Beck Herman
Palenchar & Scott LLP
• Beijing Weibu Technology
Limited Liability Company
• Boeing Co.
• Bombardier Aerospace
• CAPE
• Cascade Engineering Services
• Celestica International
• CEPREI Laboratory
• Chrysler Corp.
• CIC VIRTUHCON - the
Group 'Interphase Phenomena'
• Club Car Ingersoll-Rand, Inc.
• Cochlear, Ltd.
• CurtissWright Controls
Embedded Computing
• Daktronics Inc.
• Defense Microelectronics
Activity
• Dell, Inc.
• Dow Chemical Co.
• Dow Solar Solutions
• DSO National Laboratories
• EADS IW
• Electrospec, Inc.
• EMBRAER S.A.
• EMC Corp.
• Ericsson AB
• Fairchild Controls Corp.
• Fujitsu Network Communications
• GE Aviation Systems
• GE Corporate R&D
• GE Healthcare Technologies
• GE Intelligent Platforms
• GE Oil & Gas
• General Dynamics Advanced
Information Systems, Inc.
• Goodwin Procter
• Guardian Global Technologies Ltd.
• Hamilton Sundstrand
• Harris GCSD
• HDP User Group
• Henkel Technologies
• Hewlett Packard Co.
• Honeywell, Inc.
• iDirect
• Intel Corp.
• Jones Day
• L-3 Communications
• L3 Telemetry – East
• Lansmont Corporation
• LG Electronic, Inc.
• Littelfuse Inc.
• Lockheed Martin Corp.
• Lutron Electronics Co., Inc.
• Man & Machine Inc.
• MEI - Supply Engineering
• Microsoft Corp.
• MIT Lincoln Laboratory
• MKS Instruments, Inc.
• Moog Inc.
• MSA
• Munger, Tolles & Olson LLP
• NASA Glenn Research Center
• NASA Goddard Sapce Flight Ctr
• Naval Surface Warfare Center
• NetApp Inc.
• NIC Components Corp.
• Nokia
• Northrop Grumman
• Oak Mitsui
• Oracle America
• Ortho Clinical Diagnostics
• Park Electrochemical Corp.
• Philips Applied Technologies
• Philips Healthcare
• Philips Lighting B.V.
• Physio-Control Corp.
• QualMark Corp.
• Raytheon Co.
• Regal Beloit
• ReliaSoft Corporation
• Research in Motion, Ltd.
• Robert Bosch
• Rockwell Automation
• Rockwell Collins
• Rolls Royce Submarines
• Rolls-Royce Engine Control
Systems Ltd.
• Samsung Electro-Mechanics
• Samsung Electronics Co.
• Samsung Electronics
Semiconductor
• Sandia National Laboratories
• Savenia Labs.
• Schlumberger – WesternGeco AS
• Schlumberger Oil Drilling Services
• Science Research Laboratory
• Selex Electronics Systems Ltd
• Silicon Powers
• SORAA
• Souriau
• Stratasys, Inc.
• Super Micro Computer, Inc.
• Team Corp.
• TEKELEC
• Telcare, Inc.
• TEMIC Servicios, S.A. de C.V.
• Teradyne, Inc.
• Tessera
• Tintronics Industries
• Toyota Research Institute of N.A.
• TU CIC Virtuhcon
• U.S. Army ARDEC
• U.S. Army CECOM
• U.S. Army Research Lab.
• U.S. AMSAA
• Unison Industries
• United Technology Aerospace
• Universal Lighting Technologies
• Zentech
• Consumer and mobile products
• Telecommunications and computer systems
• Energy systems (generation/storage/distr)
• Industrial systems
• Automotive systems
• Aerospace systems
• Medical systems
• Military systems
• Equipment manufacturers
• Government Labs and Agencies