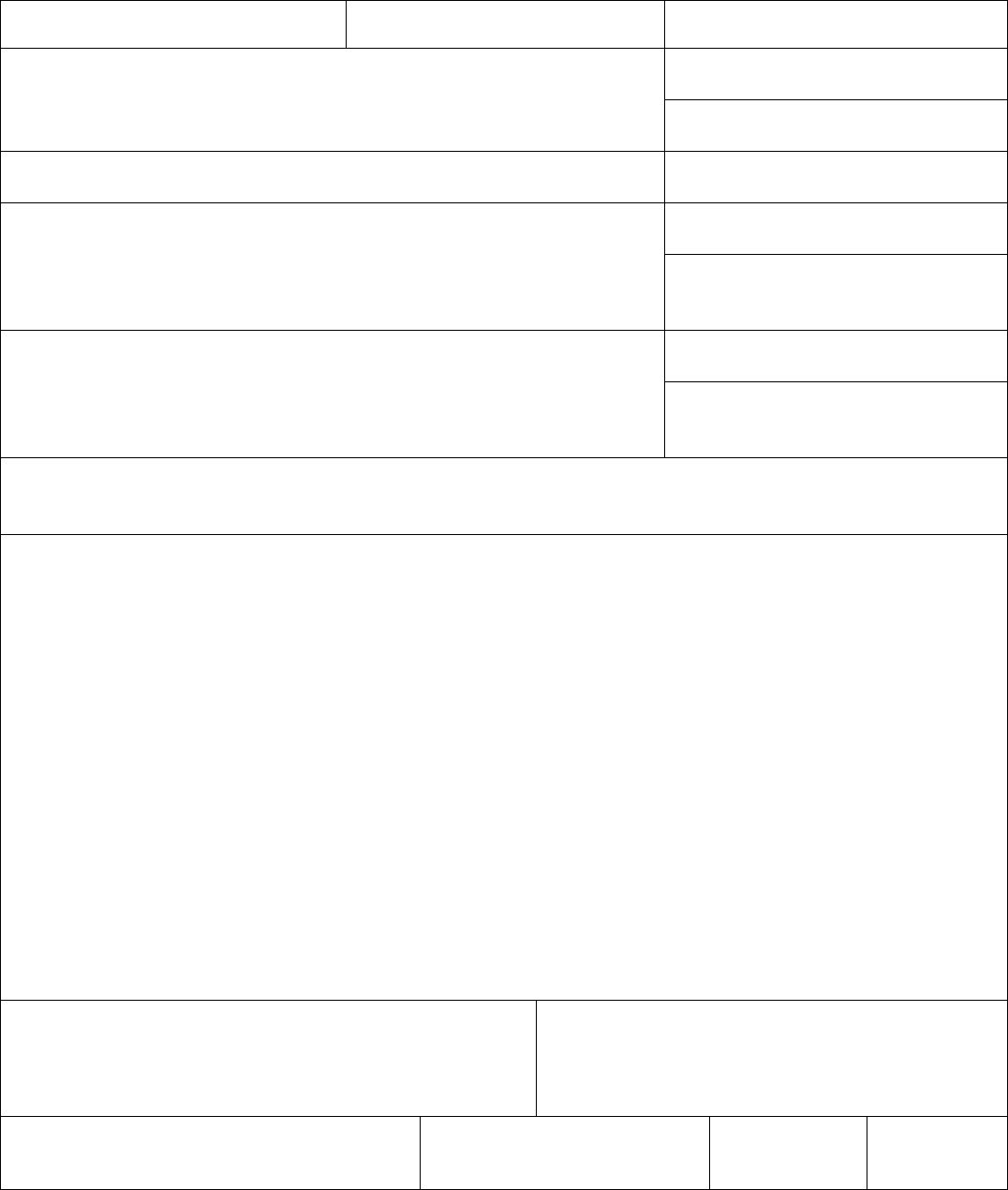
TECHNICAL REPORT DOCUMENTATION PAGE
1. Report No.
2. Government Accession No. 3. Recipient’s Catalog No.
4. Title and Subtitle
DEVELOPMENT OF HIGH PERFORMANCE CONCRETE AND EVALUATION
OF CONSTRUCTION JOINTS IN CONCRETE FLOATING BRIDGES
5. Report Date
6. Performing Organization Code
7. Author(s)
Rafik Itani, Eyad Masad, Bart Balko, Brian Bayne
8. Performing Organization Report No.
9. Performing Organization Name and Address
Washington State Transportation Center (TRAC)
Civil and Environmental Engineering; Sloan Hall, Room 101
Washington State University
Pullman, Washington 99164-2910
10. Work Unit No.
11. Contract or Grant No.
T2696 Task 02
12. Sponsoring Agency Name and Address
Research Office
Washington State Department of Transportation
Transportation Building, MS 7370
Olympia, Washington 98504-7370
13. Type of Report and Period Covered
14. Sponsoring Agency Code
15. Supplementary Notes
This study was conducted in cooperation with the U.S. Department of Transportation, Federal Highway Administration.
16. Abstract
Floating bridge concrete must be watertight, durable, workable, and must have sufficient cohesiveness to prevent segregation in
heavily congested deep walls. The mix design must experience minimal creep and shrinkage to reduce prestress losses, and
shrinkage cracking. As a result of recent concrete research, new mixes were created incorporating various quantities of fly ash,
silica fume, metakaolin, poly-carboxylate ether superplasticizers, and Caltite waterproofing admixture. This research focuses on
concrete with a water binder ratio of 0.33 and a slump in the range of 8 to 9 inches. Workability characteristics of the fresh
concrete are analyzed and hardened concrete properties tested in this research are compressive strength, chloride ion permeability,
and creep and drying shrinkage properties.
It was found that metakaolin was successful in producing mix designs with similar properties as Silica fume modified concrete.
Satisfactory strength was achieved through increasing the fly ash and lowering the silica fume contents, though, chloride ion
permeability was negatively affected. The removal of silica fume and the inclusion of Caltite decreased the concrete’s resistance to
chloride ion permeability and produced concrete that failed to attain the required 28-day ultimate compressive strength of 6500 psi.
The second part of this study focuses on developing an experimental setup to evaluate products and construction methods to help
prevent water leakage through construction joints in pontoon floating bridges. A pressure system was used to apply significant
pressures to concrete test specimens containing a construction joint. Different products and construction methods were used in
constructing the joints to determine the most effective methods for preventing water penetration in the field.
The testing results have shown compaction effort is the most important factor in water leakage through a joint. Increased
compaction in laboratory specimens leads to less water leakage through construction joints. Product selection was ineffective in
preventing water leakage if concrete compaction was inadequate.
17. Key Words
Concrete, Performance, Fly Ash, Silica Fume, Metakaolin,
Polycarboxylate, Caltite, Creep, Shrinkage, Compressive Strength,
Permeability, Construction Joint, Leakage, Waterstop, Compaction,
18. Distribution Statement
No restrictions. This document is available through the
National Technical Information Service, Springfield, VA
22161.
19. Security Classif. (of this report)
None
20. Security Classif. (of this
page)
21. No. of Pages
239
22. Price
Reproduction of completed page authorized